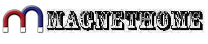
What Are You Looking For?
As we all know, electroplating the surface of neodymium magnets is a common method to extend their service life. However, when operating in humidity or sea water, the coating on the surface of neodymium magnets may also fall off or be corroded. Among them, for custom epoxy-coated neodymium magnets, salt dissolution reaction is one of the common reasons.
Next we are going to introduce some reasons that may cause the epoxy coating to peel off. We hope it will be helpful to you.
1.Improper surface preparation:
The adhesion of epoxy coatings is highly dependent on the quality of the surface preparation. If there are impurities such as oil, water vapor, and dust on the surface of the neodymium magnet, it will seriously affect the adhesion between the paint and the base layer, causing the epoxy resin to fall off.
2. Improper operation:
Neodymium magnets with epoxy plating may be subject to physical damage during use or handling, such as being struck, scratched, or bent, which may cause the coating to peel off. If the thickness of the epoxy resin coating is too thin, or the coating is exposed to water without being fully cured, it will cause the epoxy resin texture to crack and fall off.
3. Poor raw materials:
The quality of paint is directly related to the adhesion performance of the coating. If there are problems with the coating formula, production process, raw material selection, etc., such as containing volatile organic compounds and water, and inappropriate viscosity and solid content, it will easily cause the epoxy resin to fall off.
4.Bad working environment:
First of all, the construction of epoxy resin coatings requires that the ambient temperature is generally no less than 5°C. Exceeding the construction temperature range or improper air flow control may cause the epoxy resin to fall off. Secondly, in a humid environment, epoxy resin easily absorbs moisture, resulting in longer curing time or incomplete curing, which can easily lead to falling off. Finally, strong epoxy coated neodymium magnets may react when in contact with certain chemicals, causing damage to the coating. In particular, strong acids, alkalis or corrosive solutions may damage the coating.
To reduce the risk of coating peeling, choose neodymium magnets with good coating quality to ensure high durability and coating adhesion; handle magnets with care and avoid hitting, scratching or bending them; avoid Exposing neodymium magnets to chemicals such as strong acids, alkalis, or corrosive solutions, etc.
If you find that the coating of a neodymium magnet is peeling off, you should stop using it and consider recoating or replacing the neodymium magnet to ensure its proper functioning and protection, welcome to consult with professional neodymium magnet manufacturers.